Norms Restoration - 31 Seater Projects |
|
1953 Leyland OPD2/1 [2818]
2020
Mechanical Sep
- Norman Julian 2nd Sep
- Just an update on this radiator.
- 2 hours was spent stripping the paint off this.
- The paint had blisters just about all over it so it needed to come off.
- I have spent a lot of time making this aftermarket shroud fit properly.
- The old top grill bracket which I remade from the original doesn't work with this shroud.
- The radiator cap neck wasn't central with the hole so back to the drawing board to make it fit.
- This shroud also tapers in at the bottom so I had to make the grill look right with the shroud.
- There are no side mounting bolts holding this together, only the bolts at the front are needed now.
- There was also rust holes in the bottom of this shroud.
- My guess it wasn't stored right and moisture got in.
- My panelbeating and preparation skills are now required to get this shroud ready for paint.
- Also I am getting a quote from a company for getting the seals made as is.
- I'm not having any luck in finding the right size outside diameter hose.
- Robert Stevenson
- If you can find hose within a mm or so it should still work.
- As it gets compressed it will spread enough to take up the gap.
- Maybe set something up with similar sizes on the bench and see how it goes before committing to it.
- 14mm or 16mm is as close as you can get.
- 14 has to expand nearly 1.6mm. 16mm is too big.
- 1.6mm doesn't sound much but the original seals are exactly the size that is needed, 15.8 or 5/8".
- Being under some pressure it may fail.
- Norman Julian 2nd Sep
- The OPDY 2 series Leylands have 2 different style radiators.
- The one that I'm restoring is a pressed metal type over an aluminium frame that houses the tubes.
- The picture on the right has the other type which is all aluminium including the shroud.
- The steel shroud type has an area of the grill on either side cut away so you can get a spanner in there to undo the nut that holds the radiator on to the forks on the crossmember you have seen in other photos.
- To me it looks ugly as sin so I'm going to drill holes in the shroud as they did with the aluminium type.
- To make it look better I will put a rubber grommet in.
- Norman Julian 2nd Sep
- There are more holes to be welded up
- Norman Julian 12th Sep
- More work was done on this radiator shroud.
- I made some changes since the last update.
- I put a 6mm x 19mm flat bar all the way round the inner edge of the face section to lift it off the grill and to keep it looking flat when sitting on the grill.
- All the patches of bog you can see on the inside of this shroud are to fill in the fine weld gaps I did when plug welded the bars on.
- I also took away the square look and rounded the edge on each side of the recess part of the shroud at the top so as to look original.
- This frame is of 4 parts and welded together accordingly.
- It wasn't a bad job but like all welding jobs there are imperfections like high and low places that need grinding down and filling.
- There was also a lot of pitting so a lot of attention was needed to make sure all the rust was dealt with then filled. I have spent a lot of time getting the overall shape right and free of little dents etc. More sanding to be done then undercoating and spray putty to be used to get small low points I have missed.
- Then more primer and when I'm satisfied I will paint it gloss black.
- Lyndsay Holme
- So much time and effort put in to date.
- It is going to lo9k and feel absolutely fantastic when you have tightened the last bolt and applied the last lick of enamel.
- Norman Julian
- Over the years I have learnt not to muck around too much and apply filler over the whole surface with something this size and then sand about 95% off and take note of the sand through or shinny areas you can see.
- That means there are high spots.
- I keep going till I see more and larger areas which is a good thing because the filler is thin and time to stop.
- I deal with the highs with a small hammer and tap it down till it feels flat or even a little low, then fill that area again till I'm happy.
- With the lows it will fill in.
- As long as the lows are not craters it is fine.
- Normally then I can either apply a primer then a guide coat which is just a very very light spray of any paint that is a different colour to the primer.
- Then a medium grade sandpaper on a straight edge rubber pad and then start sanding off the guide coat.
- The idea is if any of the guide coat is left behind after sanding it is a low point.
- This is where the spray putty comes in.
- It will fill up the dents.
- You spray it on in layers and build it up.
- When it dries start sanding again.
- When it is level with the primer apply another guide coat over that area again and if it dissappears it is level with the rest of the surface.
- Spray putty is also good for filling in small craters left behind in welds and scratches in the metal that the primer surfacer doesn't fill in.
- This procedure is what I was taught years ago.
- I have restored a few cars using this method and it has worked.
- This shroud has many curves and is time consuming but satisfying.
- Lyndsay Holme
- Norman Julian a labour of love and patience.
- Reminds me of "Zen and the Art of Motorcycle Maintenance" from a couple of years back.
- Norman Julian
- Lyndsay Holme thanks buddy.
|
|
|
|
Last updated September 2020 |
This web site may contain Copyright material
If you find any problems with the site, please email the
Web Editor 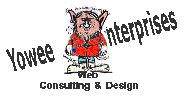 |
|