Norman Julian
This thing was taken off years ago and cleaned etc.
Today I did it again because it got oil and grease through it from the pressure clean, and also mud wasps had made a nest in there.
Norman Julian
This is the driveshaft and belt tensioner that goes ahead of the generator.
The pulleys in front of the tensioner drives all this back to the generator.
Lee Hall
Wish I lived closer mate.
I would have loved to give you a hand.
All I can say is one job at a time.
That generator is a heavy bugger 😳
Norman Julian 12th Oct
Today I put a few more things back on the engine.
Very slow going because every nut and bolt is rusty.
No zinc coating anymore. That means I have been taking every nut, flat washer and spring washer and de-rusting it.
Yes I could go and get them re-coated but that's extra expense and to be honest every nut, bolt and washer was just thrown into a bucket with other stuff.
There was odd stuff on this engine as well.
Nyloc nuts that shouldn't be anywhere near hot stuff was found.
That and other oddball stuff is what I want to change.
In these photos are a rubber hose that has fittings on either end.
It was done a few years ago to replace the other which as you can see has a joining connection roughly in the middle.
This is the oil gauge hose.
On one of the videos when I got the engine started I mentioned there was no oil pressure.
Well that's because this hose had several splits in it.
The tap you can see sits in the block with this hose and it was turned off.
Anyway, this is ready to go back on. The other picture of the pieces of copper tube is for water coming out of the block and going into that casting which carries the water to the bottom end of the radiator.
There are 2 pieces showing because I made a new one to put new fittings on.
There is an issues though.
The old coupling doesn't screw onto the new brass reducer.
Norman Julian 12 Oct
Have a look at this.
This is a fan belt tensioner for the 600 series engine.
Just marvel at the engineering that went into this.
Back in the 50s and before, they certainly knew quality.
Scott Wilson
Gen drive actually......
Norman Julian
Scott Wilson it has 2 jobs actually.
I was keeping it simple!
Norman Julian 14th oct
It wasn't at all fun putting the starter back in.
Not sure what it weighs but . . .
Anyway, it is in now and that side of the engine is all but completed.
Putting the oil tap line back on was interesting.
The tap was around the wrong way.
If it was around the right way you could turn the little tap all the way round without hitting the block.
It either was done when in the factory, or the last engine overhaul.
Simple fix though.
Just take the split pin off and spring off then turn the stopper up the other way.
If you want to know what I mean, that tappered end is supposed to go in the hose not the engine.
Tomorrow I have to sort out that water pipe then I can start the other side.
Norman Julian 17th October
Just a question for all those in the know.
I have yet to put all these parts back on the nearside part of the engine.
The question is with the exhauster.
With the engine in the TDC position, it is easier to mesh the gear on the exhauster to the engine now with the opposite side drive plate in roughly the right position for the fuel pump without adjusting to much on both the pump and the exhauster.
The question is would the mounting plate be better placed at 12/6 o'clock or at 9/3 o'clock.
If you are cluey as to know what I mean then you will understand.
Lee Hall
I think I just bolted mine on in any place from memory? The compressor isn't timed but the pump is so as long as you get the little mark for the timing in the right place that's all you need I think mate.
Norman Julian
Lee Hall yeah! I was thinking that I am at the stage of putting the compressor back in that which would be the lessor amount of adjusting has to be done.
12/6 is what I was advised.
Lee Hall
Norman Julian ah OK.
Yeah it was too long ago when I did mine.
My memory isn't that good haha. Looks like your getting dangerously close to firing her up 😁
Norman Julian
Lee Hall all of the major stuff was cleaned and sorted out ages ago.
In leaving it so long and some of it has basically lives in oil all of its life, there is a little surface rust to deal with as well as finding the right nuts and bolts and cleaning them up as well.
Also the zinc coating on all the bolts moved house many years ago, I have been painting the heads of the bolts after taking the rust off so as to look pretty rather than rusty.
Lee Hall
Norman Julian it's gonna be a gem when finished mate
Scott Wilson
Um.... Air Compressor.
Norman Julian
A little better!
Norman Julian 19 Oct
I have some good news regarding 2818 and its problem back end, as you know the previous owner was in the process of destroying this bus when fortunately the backhoe had problems and he couldn't finish the job.
It still left this mess.
I have been able to aquire a rear end section from a bus that is being broken up.
This will be a challenge but I'm pretty confident that I can do this.
All these buses were hand made and panel fitment can and will be an issue.
Anyway, this will give some hope to this bus for future prosperity.
David Day
I recognise those backhoe bucket teeth marks
Norman Julian
David Day just as well the machine broke down, otherwise I wouldn't have met you to tell me this story.
David Day
Norman your sister, Facebook and the semi all played a part as well...
Long live the semi
Graham Inskip
Great save Norman.
Phil Steele
Good thing you came upon it to save it.
Norman Julian
Phil Steele this is the bus (2818) that I wanted to restore properly from the word go.
No one knew the whereabouts or even knew if it was still around.
I found it through a photo on Facebook.
Even then the number of the bus was hidden in the shot.
I went there on a gamble.
2547 would probably be someone else's if I had found this first.
This is the bus I mostly happen to get on when I went to high school back in 1970 to 73 on the 409 route.
It had a really unique gearbox sound.
Scott Wilson
Norman Julian Um... with some help from...... 🤣
Norman Julian 19th Oct
An amazingly simple job but very gratifying.
Blind Freddy can now see that knob and sign.
I remember when I first started this bus and when I wanted to stop the engine I naturally went for the accelerator pedal.
When nothing happened I started to wonder, then I saw the knob.
Not knowing it was there, it was hard to see anyway being painted like everything else.
Now it stands out.
The knob was chrome, but it was very corroded and pitted.
I started sanding it off but it wasn't brass underneath like I expected, just steel.
Hense the reason to paint it.
I also shortened the bolts by around 12mm that holds everything on.
There was about 12 flat washers on there to build it up to where the thread was.
Hard to understand the reasoning for that.
I cleaned up the outer cable cover and then put some oil in the cable cover for lubricating the wire.
It is a lot better now.
Norman Julian
Just recently I spent 2 hrs on and off looking for the injectors for this engine.
I had cleaned up the ones for the TD5 and AEC but was frustrated as to where I had put the ones for this engine.
Getting out the manual for this engine to do something else, I noticed then that the injectors are under the tappet covers.
Bloody hell!🤣
Norman Julian 20 Oct
Today I spent around 3 hrs on getting the fuel tap back in.
Most of the time was spent on these copper pipe sections and doing some adjusting so that they aren't rubbing on the body as much as they tend to do.
The AEC was terrible. That bus had worn through in 3 areas and on these small pipes there were around 20 odd repairs over the years.
This one so far fairs not much better.
The other annoying thing was the welding of brakets to the firewall bulkhead for things like this air filter and the fuel tap, the brackets that are holding them on was welded crooked and it looked ordinary.
I did some adjusting or humouring of the air filter and now looks better.
Norman Julian 23 Oct
Another piece of the puzzle is back in.
This little compressor creates enough air to drive the brakes etc on this bus.
What I wanted to do was to get that rectangular bracket that is on the pump which faces backwards into the easiest position possible so as to connect the injection pump to it and have minimal adjustment for the timing.
That is 12/6 aclock.
That little round device which I have shown you before mounts onto the bellhousing and has 3 settings on it for "injection", "T.D.C" and off".
It is spring loaded and a pin or locating dowel is attached.
Just set it to what position you require and then you turn the engine over slowly till it locks into that position.
The flywheel has preset holes in it to catch the dowel on its rotation.
Norman Julian 25 Oct
The donor bus.
Little bit of damage but nothing that can't be mended.
Peter Hanson
Is it another "Frog" or an Underfloor, Norman? Plenty of spare seats there.
Scott Wilson
Peter Hanson Ex 2867.
I owned it from 1995 to 2010.
Sold for parts to a fellow enthusiast.
Peter Hanson
Scott Wilson Thanks Scott.
Are you back at "The Ridge" and back at work.
All the best to you and Amelia.
I just realised that it is only 2 months to Christmas.
This year has certainly flown.
It's definitely true, the older you get the quicker it goes.
Norman Julian
Peter Hanson frog
Adrian Spencer
another bus to restore Norm.
Turn it into a holiday apartment
Chris Dempsey
Any fleet number
Scott Wilson
I need rear bumper for 2866 if you don't need it.....
Norman Julian 26 Oct
Slowly but surely! The injector pump in position.
Yes I found where the filter sitting up on the bulkhead wall connects to.
In the first picture you can see where the injector pump round drive plate is sitting up flush with the compressor plate.
You can also see a flat line etched onto the round plate.
Now that line just has to be a little south of the small angled plate that has its sides cut at an angle.
The engine is locked in the INJ position on that device that is on the bellhousing.
In theory when I turn the injector pump plate around to the spot I mentioned I can lock it in with a few blots through the plates and the engines timing should be close to correct.
Norman Julian
Those 2 lines have to be nearly lined up for the timing to be close to
|
|
|
|
Last updated Oct, 2024 |
This web site may contain Copyright material
If you find any problems with the site, please email the
Web Editor 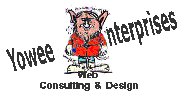 |