Norms Restoration - 31 Seater Projects
1939 Leyland TD5 [1635 DD]
2023
Mechanical November
Norman Julian
I know it has been a while since I posted anything on any of my buses.
Now though I want to get back to this project and put this engine back together.
For quite a long time, I have been waiting to get 7 replacement engine bolts done.
With covid things went quiet in the engineering sector and then there was no staff to do anything.
Now though I have the bolts back from being machined.
These are an unusual size and thread. One side is 5/8" 12tpi and the other end is 5/8" 16tpi.
Also the steel is hi tensile [4140].
The second photo shows the corrosion of some of them.
The other thing that took time was I had to get the block checked out.
In the 4th photo you can see a segment on the bottom of the block missing.
It has been missing for quite some time.
More than likely while it was still in service.
The advice given to me about welding this section wasn't at all positive.
50/50 at best.
Yes I know cast iron can be welded but it is determined on porosity of the metal, hense the 50/50 risk.
I was given an alternative though about using a liquid metal product by DEV-CON, specifically for cast iron.
When I first heard this bus running it had a blown head gasket, but it wasn't in the area of this broken section of block.
I feel confident that where the break is that if done properly it won't be an issue when the bus is running again.
Believe it or not that isn't what is scaring me.
Putting the head on is, because I just lifted it off the block without doing any prep work in regards to timing being out when I put it back on.
This is a very basic overhead cam engine.
Bugger!
Gregor Neil Robertson
Omg you need more than good luck there.
Some very careful rebuilding by experienced metal workers and ditto for timing.
Hunt them down to work with you. Sorry beyond my area of expertise.
Post up enquiries and I hope you locate the advice you need.
No doubt plenty of skilled workers in India and some in the UK.
Good luck with that!
Norman Julian
12 Nov
Interesting day today if you like going 1 step forward and 2 back.
First thing I wanted to do was to find top dead centre for the timing so as to put the head back on the gearing for the cam shaft to be in the right place.
I thought it would be easier to turn the engine over by using the crank shaft with the thread on it.
(pictured).
The only thing is you have to engage the shaft as well as turn the handle.
I was using a spanner on the nut.
It turned all the way in and kept going.
Hense the thread stripped in the nut.
I ended up using a long pinch bar on the fly wheel to turn the engine.
When I thought I had the piston in the right position, I couldn't see anything marked on the flywheel as seen in picture from workshop manual.
I got confused and got a rag in there and cleaned up the flywheel a bit and saw a mark.
I got the screwdriver and found the line scribed in the flywheel and made it that it is easy to see.
I moved onto the head.
I was wondering where the corresponding timing mark would have been on the cam gear.
Couldn't see anything.
I then found what I was looking for in the manual.
The plate behind that diagonal gear has a line scribed in it.
I think that is what I have been looking for.
Other challenges I have is the corrosion in the water pump.
The engineer guy I know seems to think that the pump is not up to scratch anymore as far as pumping water all the way around the engine.
I have to make lots of new gaskets as well.
There are 7 grease nipples that are completely missing or partially.
The one pictured is suppose to have a cap on it.
The idea is to fill the cap then screw the cap on the thread and pressure forces the grease in.
Scott Lewis
The grease heats up and melts as a liquid onto the bearing I believe my Leyland 370 has the same grease cup on the pump
Mine also has a injection mark on the flywheel also
Set up there then fit your injector pump to the mark there
Then spill time it.
photo of nut
Norman Julian
11/16 spanner fits the nut. 12tpi.
I can never work out British Standard Whitworth.
The thread looks more like 3/4".
Alan Routh
What size / pitch is it? I may have a few odd taps kicking around collection
Norman Julian
This nut is stripped out.
A unique size for which I don't have the tap to make another.
photo of brass grease nipple
Norman Julian
This grease nipple is supposed to have a thread cap.
photo of cog
Norman Julian
If you look closely you can see a scribed line behind the gear.
photo of timing mark
Norman Julian
You can see the pointer and the scribed line in this picture.
Norman Julian
7 Nov
Starting this job again after all this time is challenging.
I made 2 gaskets for these side water jacket plates.
I thought though before I sit them on I would just blow out any remaining deposits that I may have missed.
I got another considerable amount out.
I put it down to sitting there to completely dry right out that small chunks broke off the side walls of the piston housing.
Originally I got 2 and a bit kilos out and today's effort would make it 2.5 kilos or thereabouts.
I have one plate on but 1 bolt hole has stripped out.
I will have to deal with that.
I will have to drag the bus out of the shed to give the surrounding area a hot wash.
The underside of the bus looks like it has been off road.
Mud is thick and the engine needs a thorough clean before I put it back together.
3 pic
Phil Steele
Be patient and just work at a pace you like and post your progress so followers can enjoy 😁
Norman Julian
10th Nov
After doing the water jacket plates the next job I wanted to concentrate on was the water pump.
The photos here are when I pulled it out from the engine and pulled it apart and checked it out.
It was a mess but it cleaned up OK.
Today though I was looking more closely at the impeller which is apart of the pump body.
Looking through the inlet I thought the impeller looked a little far from the side of the body.
Because there is a brass plate factory pressed into the pump body, I couldn't take it off.
I took it to a guy I know who has the tools to take it off. He agrees with me about the impeller.
The pump needs to be working at peek or it won't get water pushed through its rather long distance through the engine and up in the radiator.
15 photos
Peter Velthuis
Did an awesome job on that Norm.👌
Norman Julian
Peter Velthuis thanks buddy.
pic starter mot
Norman Julian
Water pump to the lower back part of this picture behind the generator.
Direct drive system.
pic slot body
Norman Julian
This is the pump body.
You can see the brass plate and how it is pressed into the cast pump body.
I think the impeller and the inside of the body has corroded enough as the water isn't being pushed through enough to be of any use.
Norman Julian
5 Nov
Today for a few hours I retapped every bolt hole (mainly cleaning up the threads in the holes) and using the die I redone the tops of the bolts already in there.
Now if I can only remember which bolt goes where! 🤣 I'm thinking I may take them all out and start from scratch when I sit the head flat on the block.
Well not exactly sitting it on the block rather 10mm or so above.
Don't want to damage the head gasket when it isn't aligned properly with the block.
This head weighs a mighty lot.
pic head bolts
Norman Julian
16th Nov
This inner mechanism has a bearing on either side of that piece with the channel.
In the middle of that channel there is a hole (out of picture).
The other pump in a picture you can see a semi circular bracket that has a grease nipple on in that is brass.
When a grease gun is attached to that nipple grease is forced down and along that channel till it reaches that hole that I mentioned.
Grease under pressure gets forced into that hole and lubricates the 2 bearings.
I hope that is understood.
pic bear
Norman Julian
This is the pump drive.
We think that it sits on a ceramic piece under that to form a seal and resists a lot of heat.
On the inside is an impeller.
pic of drive
Norman Julian
17th Nov
Today I pulled apart the mechanicals in this waterpump.
That meant taking the drive bar off which is pressed on.
To do that I had to make a special puller.
It was still a little unco-operative so a little heat was introduced and that fixed the problem.
The news with the pump body which contains the impeller was not what I wanted to hear.
The guy I took it to who is really good in most things wasn't able to separate the brass piece which has the impeller from the cast iron body.
More than likely some part of it would break trying to separate.
Both pumps did the same thing.
The rest of the pump came apart so I soaked it in petrol and gave it a good clean.
The rest of the mechanical body came up well with a bit of treatment on the wire wheel.
Norman Julian
20th Nov
I wonder if anyone might know what this thing is.
The manual I have doesn't show it and neither does the TS7.
It is just a container that sits on the side of the head.
It is empty.
To me it looks like it does nothing but I am thinking that it may have one stage had a strainer in it to maybe stop contaminants from circulating through the engine.
It basically connects to the top of the radiator.
If you may know please comment.
photo
Scott Wilson
Thermostat housing.
Norman Julian
Scott Wilson ah! Thanks!
Brian Blunt
Got a similar device on one of our petrol engines, but not the other.
The outlet on the side made us wonder if it was a connection for a heater unit?
I forget where the pipe on the flange went to, runs around the back of the block somewhere.
pix54
Norman Julian 28 Nov
A few more things revisited.
The round long black thing is a fuel filter.
When I first worked on it, I cleaned it up and I forgot to apply a film of diesel inside so it formed a layer of surface rust.
Today I removed the rust and applied diesel on the inside to keep it protected.
The air filter was given a new centre thread and I made a special type of wing nut so it will never on its own come loose and have a rattly lid.
The last one was the auto-vac.
The last time I worked on this I reconstructed the screw-on lid where you put the fuel in.
I polished up the brass mechanism but I never did anything with the inside.
It was corroded badly.
There were little holes that were in it from the corrosion so I repaired them but left the rest.
Today I applied a layer of rust converter to the inside.
Tomorrow I will get rid of any loose and flaky metal.
Once all the loose material is gone, it will get the treatment.
Rusty Williams
Perfection again.
|
|
|
|
Last updated November, 2023 |
This web site may contain Copyright material
If you find any problems with the site, please email the
Web Editor 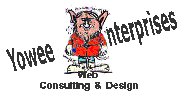 |