Norms Restoration - 31 Seater Projects
Workshop
2022
March
Norman Julian 17 Mar
Just a little update.
I want to start putting some of the rear panels back on the bus but I have to remake a few first.
Quite a few of the originals have bullet holes in them and I don't want that.
I bought this new beading machine a while back and I did press some panels out but the die that came with it wont fit the bill unfortunately with this bus.
Also a while back I got this very old bead or swaging machine which resembles a hand wringer (if anyone remembers what they looked like all those years ago) the dies that are in the machine are the right ones.
The other day I went to see if I could get new dies the same profile as the old machine made up to fit the new motorised machine.
Yes that is possible but 3 months was the waiting time.
The cost was up there as well.
I thought about it and now I will make a stand for the old machine to sit on and use it.
These old machines normally require 2 people to operate them properly.
I will see if I can operate small jobs on my own.
Anyway, the stand that I am making will look similar to the other machine.
The tricky part is how I will get it to sit in the stand and be stable.
The shaft at the very bottom is I think made for 2" pipe which you can't get anymore.
What I have started to do is by using 6mm plate and cutting the same size dimensions as the square plate around that shaft is to have a snug fit so as to sit on the stand and not move.
You can see that it is out of balance so a tight or snug fit is required.
There will be 2 plates made the same with space in between so as to spread the load.
The first plate (as pictured) is cut and the hole is cut very snug so as to give the shaft no sideways movement at all.
I feel that this will work.
Norman Julian
Wasn't a quick job making this hole.
I have no metal hole saw that can drill steel this thick.
I just used a drill bit and drilled a series of holes near the line I wanted and filed the rest.
I have done one and one to go.
David Wilson
fabricate a guide to set the panels the correct distance.
Use two hands to guide the panel and have someone wind the handle.
For vertical swages, cut the panel slightly wider and then trim off in the guillo
Gregor Neil Robertson
Great to have the right tools! Well done.
Norman Julian 26 Mar
The beading machine stand is now near finished.
It sits well and it doesn't wobble around due to the careful amount of time I spent on the 2 plates the bottom spindle sits it.
The frame itself took no time at all to make.
I based it on the original machine I have.
I will make a few pegs and weld them onto the main post to take the 2 other dies that came with it.
I gave it a test run and it works fine but it is a 2 man job I think when doing large pieces.
Ben Summers
If only I had your skill level, Norman!
Norman Julian
Ben Summers no skill in making this buddy!
Ben Summers
I'm speaking as someone with no welding skills.
Norman Julian 27 Mar
Well she is done now.
A few things I may have to go back to.
I bought a pack of castors and there were 2 locking and 2 non locking wheels.
In hindsight 4 locking wheels would be better or at least 1 on the back and one on the front instead of 2 on the rear.
I'm glad that I had the other more modern one because it is hard to know what the ideal working height for one of these may be.
The height I have it is ideal for me as it turns out.
I put 5 pegs on for dies and things.
I did a practice shot with this machine but I will have to get the ideal amount of pressure to match the 2 prewar buses that have the same pressings.
Robert Stevenson
I fitted a motor to my hand operated one.
Makes life a lot easier.
Norman Julian
Robert Stevenson It would be like putting a diesel engine into a chariot! LOL
|
|
|
|
Last updated March, 2022 |
This web site may contain Copyright material
If you find any problems with the site, please email the
Web Editor 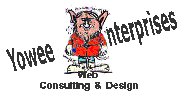 |